燃煤电厂量世界第一 中国如何治理烟气?
导语:中国雾霾的首要来源是燃煤排放的二氧化硫和氮氧化物,单塔一体化脱硫除尘深度净化技术在一个塔中同时实现深度脱硫除尘,高效、能耗低
导语:中国雾霾的首要来源是燃煤排放的二氧化硫和氮氧化物,单塔一体化脱硫除尘深度净化技术在一个塔中同时实现深度脱硫除尘,高效、能耗低、适应性强、工期短、操作简便且不额外增加占地。而且,它的脱硫和除尘效率都非常高,彻底消除了“石膏雨”问题。
转载自网易新闻学院(we_know_media)
出品| 网易新闻
作者| 天地流皓,浙江大学材料科学博士
每到供暖季,雾霾成为北方许多地区逃不开的话题。根据目前许多科学家的研究,“烧煤”中排放的二氧化硫和氮氧化物是中国雾霾的首要来源。
然而现阶段以及未来相当长的一段时期内,中国的能源结构仍然以煤炭为主,火电厂是燃煤的消耗大户,要缓解“十面霾伏”的状况,就不得不考虑电厂燃煤的脱硫处理问题。
今天我们要介绍的单塔一体化脱硫除尘深度净化技术(SPC-3D)正是这样一种技术。
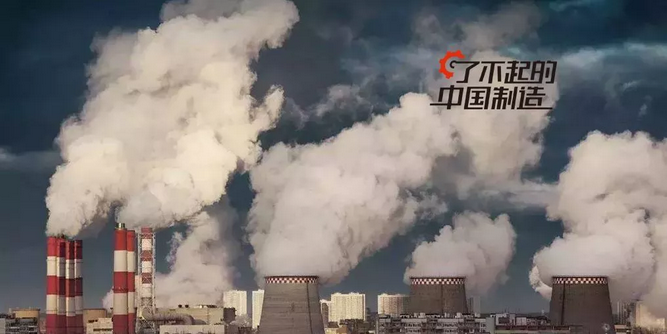
(一)常规的改造方案为什么让电厂难以接受?
随着对环保的日益重视,目前中国几乎所有燃煤机组均配备了基本的脱硝脱硫除尘装置,煤炭燃烧后所产生的烟气会先后经过脱硝装置、静电式除尘器、吸收塔脱硫处理后再排放到大气中。
然而,烟气经过传统的处理装置后,污染物浓度仍远超过最新的超低排放标准,且目前大部分的脱硫装置还存在严重的“石膏雨”问题。为了达到超低排放标准,现在所有的燃煤机组的烟气处理装置几乎都需要进一步改造优化,其中关键的重点和难点在于改造脱硫和除尘工艺。
目前常规的改造方案是对原有静电除尘器进行多处改造,然后在吸收塔后增加庞大的湿式电除尘器来进一步除尘,而脱硫工艺则需要采用两套或类似两套吸收塔来实现,这种方案类似于面多加水,水多加面,无外乎是为了降低污染物的浓度增加吸收装置的数量。
而且,湿式电除尘器和增加新的吸收塔都存在占地面积大的问题,除硫处理改造难度也极大。所以整个常规技术改造的投资高,工期长,改造难度大,场地受限制,运行费用也高,大多电厂仍然很难承担这种常规技术改造带来的损失。
如果能够不对已有的静电除尘器进行多处改造,且不增加额外的湿式电除尘器和新的吸收塔,那么改造的投资将会大大降低,工期也可以大大缩短,那么,在单个吸收塔内做到同时深度脱硫除尘有可能么?
在2014年7月,中国开发出单塔一体化脱硫除尘深度净化技术(SPC-3D技术),该技术在一个吸收塔内同时实现脱硫效率99%以上,除尘效率90%以上,满足了二氧化硫排放35mg/Nm3、烟尘5mg/Nm3的超低排放要求。
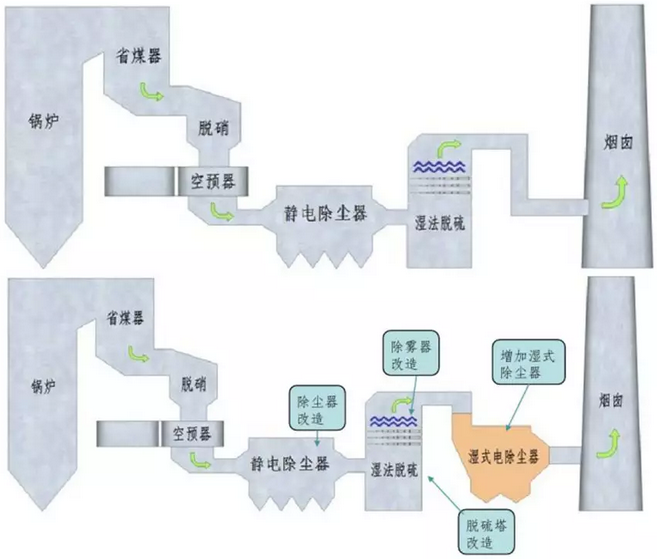
(上图为传统的燃煤电厂烟气治理装置;下图为欲达到超低排放标准的常规改造方案)
(二)单个吸收塔如何同时做到深度脱硫除尘?
运用SPC-3D改造的烟气处理装置如下图所示,只需改造已有的吸收塔即可实现超低排放,不需要对原有静电式除尘器进行改造,也不需要增加湿式电除尘器和新的吸收塔。
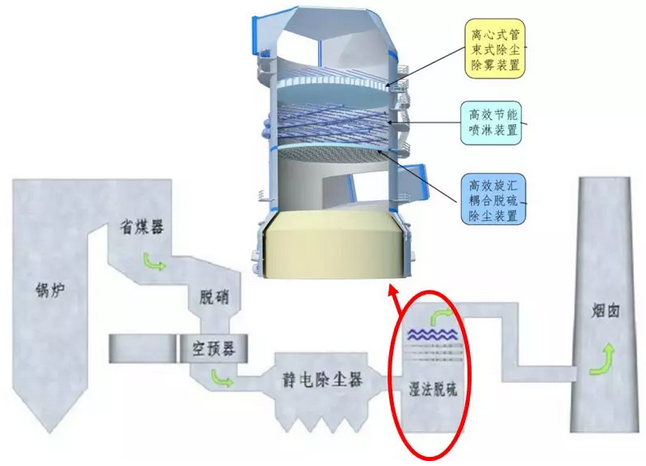
(采用SPC-3D技术的改造方案)
其主要是在原有吸收塔内加装旋汇耦合装置,改善原有喷淋层结构和喷嘴布置方式,并且用管束式除尘除雾装置代替了传统的除雾器。
SPC-3D的三大技术核心包括旋汇耦合高效脱硫除尘技术、高效节能喷淋技术和离心式管束式除尘技术,它们在吸收塔内从下至上分布。
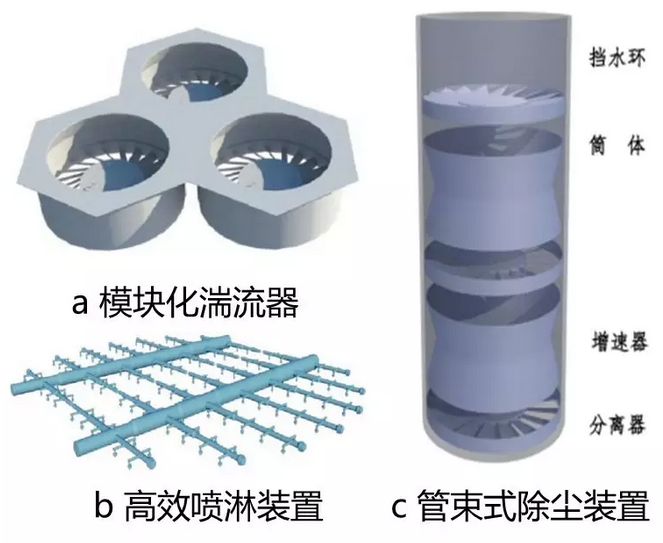
(SPC-3D三大核心技术的核心部件)
尽管从科学角度来看,脱硫过程也就是SO2和石灰石浆液反应生成硫酸钙的过程,不过几个化学方程式而已,但是工程上想要用尽可能少的浆液去吸收尽可能多的SO2却不是一个简单的问题。
我们都知道,化学上两种物质想要反应完全首先要充分接触,物质的比表面积越大对反应促进作用就越强,这也是面粉粉尘为什么会爆炸的原因。
传统的吸收塔(空塔)直接将烟气通入塔中和喷淋的浆液接触,然后被吸收,烟气的分布十分不均匀,造成很大一部分浆液都浪费了,所以需要两个塔甚至更多才能达到脱硫目标。
而旋汇耦合高效脱硫除尘技术则是先对进入塔内的烟气进行一定的处理,即在引风机出口的烟气进入吸收塔后,首先经过由模块化湍流器构成的旋汇耦合装置。根据流体动力学原理,烟气会与浆液混合形成强大的可控湍流空间,使气(SO2)、液(浆液)、固(烟尘)三相充分接触,提高了气液固三相传质效率,完成了第一步的脱硫除尘。
而加装模块化湍流器相比空塔则实现了快速降温及流场均布,可以有效避免喷淋气流分布不均,喷淋层失效的问题。
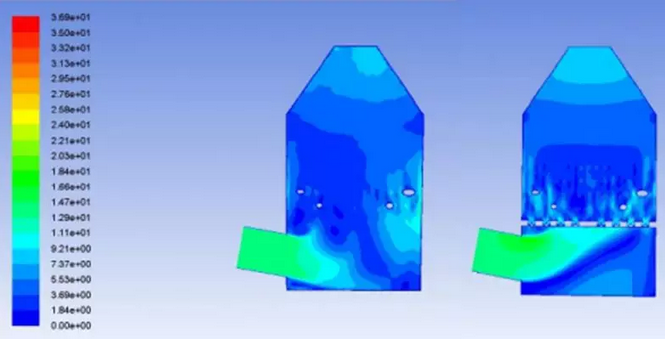
(有无湍流器的吸收塔内速度分布对比,左边是无湍流器,右边是有湍流器)
高效节能喷淋技术则是通过优化喷淋层结构,改变喷嘴布置方式,开发新型喷嘴从而大大提升自身雾化效果,这些优化大大提高了浆液覆盖率,增大了气液接触的面积。经过旋汇耦合装置后的烟气接触到喷淋的浆液,即完成第二步的洗涤,可以实现SO2的深度脱除和烟尘的二次脱除。
尽管SPC-3D只采用了单个吸收塔,但当烟气经过高效旋汇耦合装置和高效节能喷淋装置两次洗涤反应后,已经基本实现了深度脱硫目标,可以达到SO2的超低排放标准了,总的脱硫效率是湍流器效率和喷淋层效率的叠加。
而除尘除雾主要靠管束式除尘技术来完成,当经过上面两个装置的烟气进入管束式除尘除雾装置后,烟气首先通过底部的分离器,产生高速离心运动,在离心力的作用下,液滴和烟尘向筒体壁面运动,在运动过程中相互碰撞、凝聚成较大的液滴,液滴被抛向筒体内壁表面,被壁面附着的液膜层捕获,实现粉尘和雾滴的深度脱除。
管束式装置中还可以采用多级分离器,实现对不同粒径烟尘颗粒和液滴的捕获。分离器之间可以设置增速器,提升气流的离心运动速度,并维持合适的气流分布状态,从而控制液膜厚度及气流的出口状态,防止液滴的二次夹带。
从上面的介绍中我们了解了SPC-3D技术的工作原理,可以看到,在一个塔中同时实现深度脱硫除尘是脱硫和除尘装置精心设计的结果,它对于脱硫和除尘是相互耦合和叠加的,正是这种优化的设计组合保证了污染物的超低排放。
(三)单塔一体化脱硫除尘技术有何独特之处?
SPC-3D技术一经推出便得到电厂、监测单位、国家环评权威部门的一致好评,这与其独特的优势是分不开的。
首先,该技术脱硫和除尘效率都非常高,可以实现单塔高效脱硫除尘,而且彻底消除了“石膏雨”问题。
以某300MW电厂为例,可以看出运行过程中脱硫效率不低于98.8%;当吸收塔入口处烟尘浓度在50mg/Nm3以内时,出口烟尘浓度可以持续保持≤5 mg/Nm3。

(山西某300MW电厂运行过程中数据监测)
其次,该技术的系统适应性很强,运行过程稳定可靠。受惠于旋汇耦合装置超强的传质能力,当烟气中含硫量波动时,系统脱硫效率仍能保持稳定,且随着机组负荷增加喷淋层的脱硫效率逐渐降低,旋汇耦合装置的脱硫效率则逐渐提高,总的脱硫效率变化较小,这也就是说整个系统的脱硫效率十分稳定。
这一特色使得它不必为高硫煤种额外改造,对中国的丰富煤种国情十分适用。另一个可观的地方是系统内为固定安装的静止设备,检修维护十分方便,所以整个系统运行起来十分稳定。
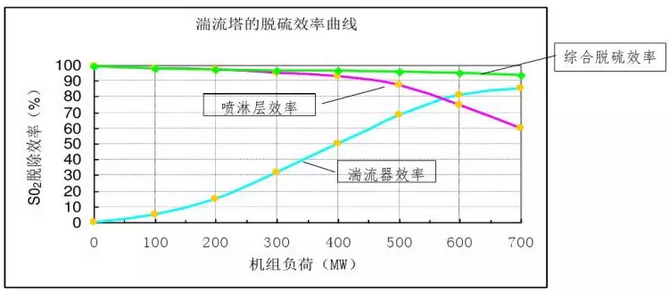
(烟气入口SO2为2500mg/Nm3的600MW机组系统的脱硫效率曲线)
此外,SPC-3D技术改造投资比常规技术低30-50%,也不会额外增加用地面积,减少电力企业投资压力。运行过程相比常规改造技术节能效果显著,整体运行费用(包括投资成本)仅是常规加装湿式电除尘技术的15%-30%。
这主要是基于旋汇耦合装置良好的均气效果、超强的传质能力和长的烟气停留时间,所以运行中的液气比很低,浆液循环量也因此大幅降低,还有管束式除尘装置不需要用电,所以综合电耗至少可以降低30%。
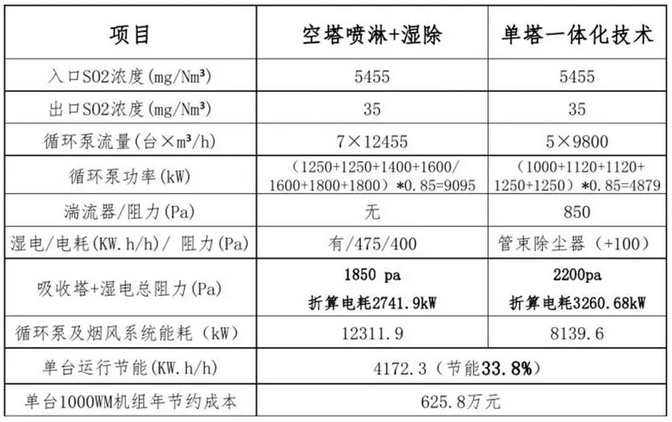
(以1000MW机组为例,采用单塔一体化技术和常规的空塔喷淋加湿除能耗对比)
另外,采用SPC-3D技术改造工程量小,整个改造工期短,直接利用原有吸收塔改造,不改变吸收塔外部结构,不用增加庞大笨重的湿式电除尘器,布置简洁,相比于常规改造至少需要60天,采用SPC-3D技术整个改造工期只需要20-30天。
最后,基于大量长期数据发现SPC-3D技术对机组排放的SO3脱除效率达到约86%,远远高于其他技术。而且,它还对液滴和重金属汞等具备协同脱除作用。
结语
SPC-3D技术能在单个吸收塔内实现脱硫除尘除雾,达到国家制定的超低排放标准。其单塔高效、能耗低、适应性强、工期短、操作简便和不额外增加占地等巨大优势大大减轻了电力企业改造压力,对中国实现火电全面超低排放起到重要推动作用。
转载自网易新闻学院(we_know_media)

责任编辑:李鑫
免责声明:本文仅代表作者个人观点,与本站无关。其原创性以及文中陈述文字和内容未经本站证实,对本文以及其中全部或者部分内容、文字的真实性、完整性、及时性本站不作任何保证或承诺,请读者仅作参考,并请自行核实相关内容。
我要收藏
个赞
-
西北光伏市场分析: 七大经验、四大问题、五大原因、破解弃光三大举措
2018-12-24光伏市场分析 -
拍卖 | 浙江丽水龙泉周调源电站的电站资产 2019年1月7日开拍(变卖)
2018-12-24水电站拍卖 -
太离谱,光伏9.3元/瓦中标!?
-
中国沿海电煤采购价格指数(CECI沿海指数)第54期
2018-12-21电煤采购价格 -
2019年电力行业年度投资策略报告:火电走出低谷 核电方兴未艾
-
2018年工业锅炉行业发展现状与2019年行业前景分析【组图】
-
拍卖 | 浙江丽水龙泉周调源电站的电站资产 2019年1月7日开拍(变卖)
2018-12-24水电站拍卖 -
三峡水电站年发电量首破一千亿千瓦时,相当于节煤0.3亿吨
2018-12-21三峡水电站 -
17个水电项目!湖南省发改委关于安化县友谊水电站等水电站上网电价的批复
2018-12-20水电上网电价